Welcome to zhongshan shengerfu Hardware Technology Co.,Ltd
The ProfessionalMetal & Plastic Parts manufacturer
High-Precision Die Casting, CNC Machining, Injection Molding & Stamping Services from Zhongshan Saint Rich Hardware Technology Co., Ltd.
Years of Experience
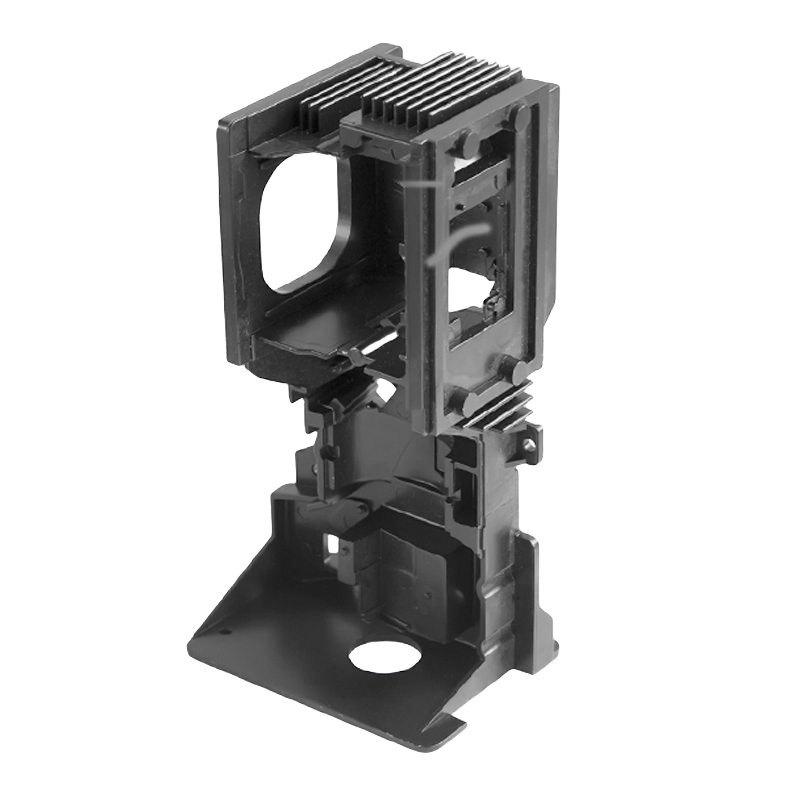
Best Award Product
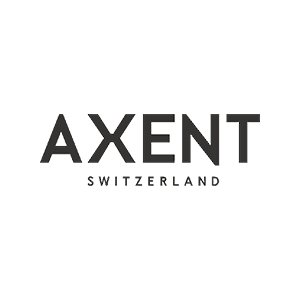
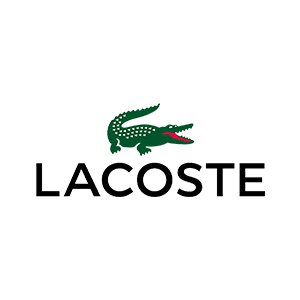
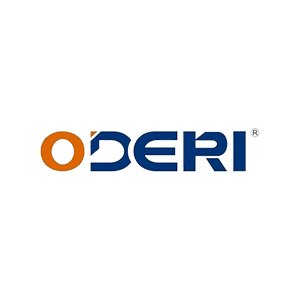
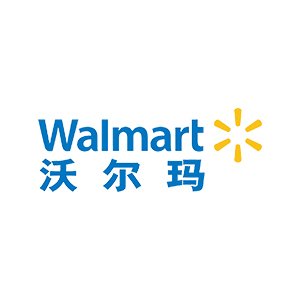
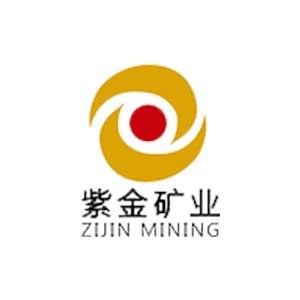
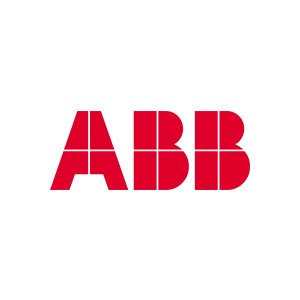
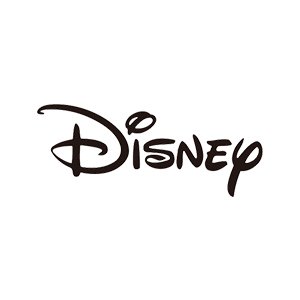
Your Trusted Manufacturing Partner – Saint Rich
At Zhongshan Saint Rich Hardware Technology Co., Ltd, we specialize in high-quality die casting, plastic injection molding, metal stamping, CNC machining, and custom mold development. With over a decade of experience serving OEMs, wholesalers, and industrial clients across North America, Europe, and Australia, we deliver precision-engineered parts that meet your exact specifications.
We’re committed to fast lead times, competitive pricing, and strict quality control for every order.
Affordable Price
Precision and Accuracy
Consistent Quality
Increased Productivity
Why Saint Rich is Your Ideal Manufacturing Partner?
ISO-certified facilities & quality management
Flexible production volume – from prototypes to mass production
Serving a wide range of industries: automotive, electronics, consumer goods, etc.
Strong engineering support & fast prototyping
Export-oriented – fluent in international standards and packaging
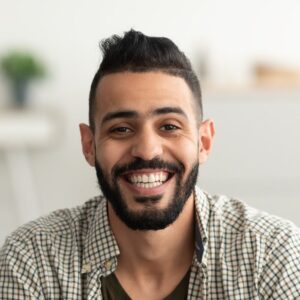
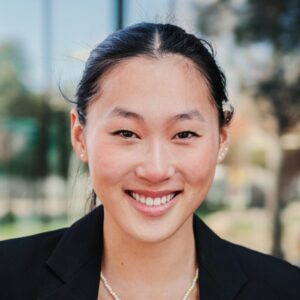
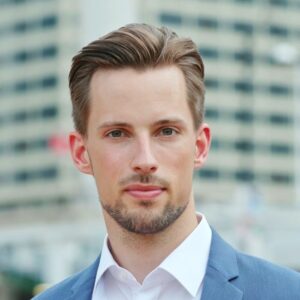
Active client with positive reviews
Custom Parts for Global Industries
We provide reliable custom-manufactured parts for:
Automotive | Consumer Electronics | Industrial Equipment | Home Appliances | LED Lighting | Furniture Hardware and more.
Our Services
Parts Manufacturing Services
Our Core Manufacturing Services
Die Casting
Aluminum and zinc alloy die casting with excellent dimensional stability and surface finish.Plastic Injection Molding
Custom plastic components with a variety of materials, colors, and tolerances.CNC Machining
Precision milling, turning, drilling, and surface finishing with advanced CNC equipment.Metal Stamping
High-volume metal forming with tight tolerances and consistent quality.Custom Mold Making
End-to-end mold design and fabrication for both plastic and metal parts.
Die Casting
Share with you the production capacity of first-class suppliers of listed enterprises, mass customization of non-standard parts, support hot chamber and cold chamber die-casting, sample reproduction, and provide material certification, inspection and measurement reports.
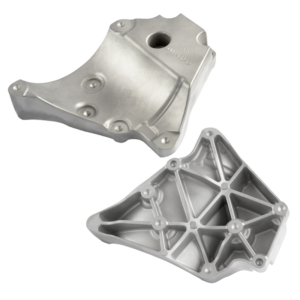
Injection Molding
Injection molding is the most economical method for mass producing plastic parts. Lipu provides on-demand prototyping and production tooling services, focusing on customer-centric services. We connect you with the best injection mold suppliers in our network to meet your specific needs while ensuring that design and cost are not compromised.
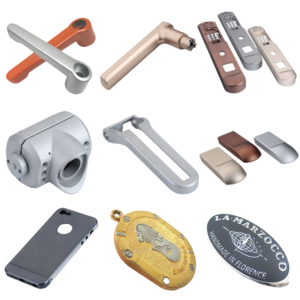
CNC Machining
Provide a variety of complex CNC machining services to help you quickly prototype and mass production. Quick proofing of non-standard parts Up to 48 hours to complete production CNC milling, turning and drilling
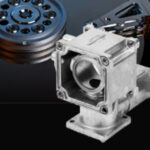
Mold Manufacturing
Although mold manufacturing requires a greater investment than tooling designed for prototyping or small series production, it is important to understand the differences between them. Saint Rich uses industry-leading technology and processes to manufacture all types of molds for you.
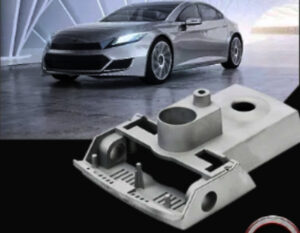
Let’s Build Your Next Project Together
Whether you need high-precision aluminum die cast parts or custom plastic molds, Saint Rich is here to deliver fast, reliable, and cost-effective solutions.
Our Blog
Latest News & Updated
Frequently Asked Question
Q1: What materials are commonly used in die casting?
A: The most common materials are aluminum alloys (e.g., ADC12, A380), zinc alloys (e.g., Zamak), and magnesium alloys. Each offers a balance of strength, weight, and cost.
Q2: What is the typical tolerance for die-cast parts?
A: Standard tolerance is ±0.1mm for dimensions under 100mm. Tighter tolerances (±0.05mm) are possible but may increase costs.
Q3: How does surface finish affect die casting?
A: A smooth surface finish reduces post-processing (e.g., polishing) and improves aesthetics. Rough finishes may require additional steps like machining or coating.
Q4: What factors influence die casting costs?
A: Key factors include mold complexity, material type, part size, production volume, and post-processing requirements (e.g., anodizing, powder coating).
Q1: What is the minimum order quantity (MOQ) for injection molding?
A: MOQ depends on mold complexity, but typically ranges from 1,000 to 10,000 pieces. Prototype molds may allow smaller batches.
Q2: How long does it take to produce an injection mold?
A: Lead time varies from 3-8 weeks, depending on mold complexity, material availability, and design revisions.
Q3: Can you handle overmolding or insert molding?
A: Yes. Overmolding (combining multiple materials) and insert molding (embedding metal/plastic parts) are possible with proper mold design.
Q4: How do you prevent warping or sink marks in plastic parts?
A: Optimizing cooling channels, adjusting gate locations, and selecting materials with low shrinkage rates (e.g., ABS, polypropylene) help minimize defects.
Q1: What is the difference between CNC milling and turning?
A: CNC milling uses rotating tools to remove material from a stationary workpiece, while CNC turning rotates the workpiece against a fixed cutting tool.
Q2: Can you machine hardened metals like stainless steel or titanium?
A: Yes, but it requires specialized tooling (e.g., carbide or diamond-coated tools) and slower machining speeds to avoid tool wear.
Q3: What surface roughness (Ra) can you achieve?
A: Standard machining achieves Ra 3.2–6.3 μm. Precision grinding or polishing can reach Ra 0.4–1.6 μm.
Q4: Do you provide GD&T (Geometric Dimensioning and Tolerancing)?
A: Yes. We follow ASME Y14.5 standards to ensure parts meet specified geometric tolerances.
Q1: What material thickness can your stamping process handle?
A: Typically 0.5mm to 6mm for metals like steel, aluminum, and copper. Thicker materials may require progressive dies or multi-stage stamping.
Q2: How do you ensure consistency in high-volume stamping?
A: Automated presses, precision tooling, and regular quality checks (e.g., CMM measurements) ensure consistent output.
Q3: Can stamped parts include bends or embossed features?
A: Yes. Features like bends, holes, and embossing can be integrated into the die design.
Q4: What is the cost difference between single-stage and progressive dies?
A: Progressive dies are more expensive initially but reduce labor costs for high-volume production. Single-stage dies suit low-volume runs.
Q1: What materials are molds typically made from?
A: Common materials include tool steel (e.g., P20, H13), aluminum (for prototypes), and hardened steel (for high-volume production).
Q2: How many cycles can a mold withstand?
A: Aluminum molds: 10,000–50,000 cycles. Steel molds: 500,000+ cycles, depending on material and maintenance.
Q3: Can you modify an existing mold for design changes?
A: Yes, but modifications (e.g., adding/removing features) may require welding, re-machining, or EDM (electrical discharge machining).
Q4: Do you provide mold flow analysis?
A: Yes. We simulate filling, cooling, and warping to optimize mold design and prevent defects.